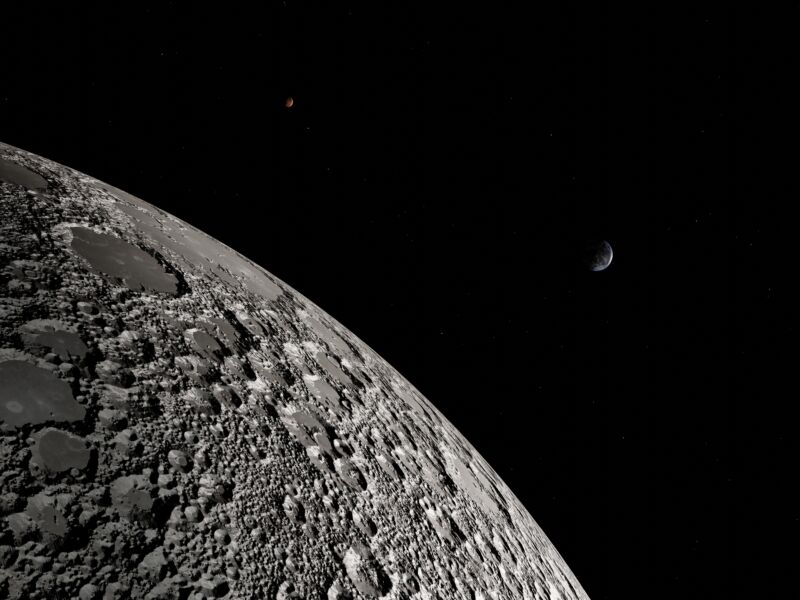
The Moon is slated to be our next frontier. When Artemis 3 takes off (tentatively) near the end of 2025, it will be the first mission since the Apollo era to land humans on our satellite. By then, there might be a new way to get around on the Moon’s gray dust, which could at least mitigate damage from sharp particles of lunar regolith.
An international team of researchers with the ESA PAVER project has figured out a way to melt Moondust—or at least an ESA-developed stimulant for it—with lasers. The researchers fired laser beams at lunar soil to create interlocking pavers that could be used to construct paved roads and landing pads. The hardened molten regolith is tough enough to withstand the weight of rovers and other spacecraft with minimal dust kickup, and it could all be made right there on the Moon.
“This technology is envisioned to play a major role in the first phase (survivability) of lunar infrastructure and base development, and over time to contribute to all phases of lunar exploration,” the researchers said in a study recently published in Scientific Reports.
Scratching the surface
Moondust has been the bane of lunar spacecraft and astronauts for a reason. On Earth, rock, glass, and other materials in soil are constantly exposed to weathering forces such as wind, rain, and flowing water, which is why grains of sand are often smooth around the edges. Lunar regolith hardly weathers because of the lack of wind and liquid water. Any spacecraft that lands on or traverses the Moon is at risk from the dust it kicks up because unweathered shards of rock and glass can easily scratch sensitive instruments and wear away at surfaces. Low gravity on the Moon also means perturbed shards keep flying around and getting into everything.
The PAVER scientists wanted to devise a method of creating paving materials from resources already available on the Moon. Shipping supplies from Earth is expensive and inconvenient, so in situ production is preferred whenever possible.
The main difference in these simulation experiments (besides the regolith simulant) was that a CO2 laser was used to heat the material instead of the concentrated solar light that would be used by astronauts on the Moon.
Stepping stones
Laser beams of different sizes and strengths needed to be tested to find the one that would produce the strongest paving material. During this process, the research team found that any crisscrossing or overlap of laser beams could lead to internal cracking, especially since lunar regolith is full of glass and other silicates. The laser that proved most effective ended up having a 45 mm (about 1.8 inches) beam that could move over dust in a specific pattern that produced triangular shapes. It melted the regolith simulate into 250 mm (close to 10 inches) pieces that were 15 mm (a little over half an inch) thick and could easily interlock with each other. Of course, these must be scaled up for actual lunar operations to accommodate actual spacecraft.
Regolith that had been irradiated and cooled had three different layers. The top layer, a type of glass, and crystallized material in the middle layer had both been melted. The thin layer of material at the bottom was sintered rather than melted, meaning it was the product of dust sticking together into a porous mass. While this material was dense and strong enough on its own, the geometric shapes designed by the scientists were meant to maximize its flexibility and resistance to cracking or breakage.
To see if they could take the weight of a spacecraft, the triangles were subjected to compression tests to see how much pressure they could take before they broke, with the highest being 216.29 megapascals (slightly over 30,000 pounds per square inch). For comparison, the Apollo lunar module weighed 33,000 pounds, and its weight was distributed over far more than an inch.
The scientists admit that there is still progress to be made in this research. A lens to concentrate sunlight would substitute for a laser on the Moon, so that should be tested. Still, those tests are worth pursuing since only a few pieces of lightweight equipment are needed to carry out this process on the Moon. It might even be possible to get them there in time for the first boots since Apollo 17 to walk on the Moon again.
Scientific Reports, 2023. DOI: 10.1038/s41598-023-42008-1