Bad news if you want to move to the moon or Mars: housing is a little hard to come by. Fortunately, NASA (as always) is thinking ahead, and has just shown off a self-assembling robotic structure that might just be a crucial part of moving off-planet.
Published today in Science Robotics, the paper from NASA Ames Research Center describes the creation and testing of what they call “self-reprogrammable mechanical metamaterials,” which is a highly precise way to describe a building that builds itself. The inevitable acronym for it is “Automated Reconfigurable Mission Adaptive Digital Assembly Systems,” or ARMADAS.
“We think this type of construction technology can serve a lot of very general applications,” lead author Christine Gregg told TechCrunch. “In the near term, the robust autonomy and lightweight structures of our approach strongly benefit applications in austere environments, like the lunar surface or space. This includes lunar surface construction of communication towers and shelters, which will be needed before astronauts arrive, as well as on-orbit structures like booms and antennas.”
The basic idea of the self-building structure is in a clever synergy between the building material — cuboctahedral frames they call voxels — and the two types of robots that assemble them.
One type of robot walks along the surface with two legs, seemingly inspired by our own biology’s kinesin transport molecules, carrying a voxel like a backpack. When that’s put in place, a fastening robot that lives in the frame itself like a worm slithers over and tightens the reversible attachment points. Neither one needs a powerful sensing system, and the way they work means high precision is not required either.
You can see a pair of walkers and a fastener worm in most of the images in this post. And here’s a transport walker handing off a voxel to a placement walker, with the fastener bot lurking below waiting to go over and lock the frame into position.

Two robots exchange a structural element while a third waits below to affix it to the lattice. Image Credits: NASA
The shape of the pieces allows them to be attached at various angles while maintaining good structure strength. You probably wouldn’t want to store rocks on top of a dome made out of these things, but they’d be excellent as a base on which to add insulation and sealant to make a dwelling.
“We think this type of construction is particularly suited to long duration and/or very large infrastructure, including habitats, instrumentation or any other infrastructure on orbit or the surface of the moon (utility towers, vehicle landing facilities),” said co-author Kenneth Cheung. “For us, the structures and all of the robotic systems are resources that can be optimized over space and time. It looks like there will always be situations where the optimal thing is to leave just structure in place (and perhaps visit to inspect it with a robot periodically), so we started with that.”
The pieces themselves could also be constructed on-site, Gregg noted:
“The voxels can be made from many different materials and manufacturing processes. Eventually, for space applications, we would like to make voxels from materials we find in situ on the moon or other planetary bodies.”
Of course, these videos of the robots at work are highly accelerated, but unlike work in a factory or sidewalk, speed isn’t necessarily of the essence when it comes to building stuff in space or on the surface of another planet.
“Our robots can work faster than shown in this paper, but we didn’t see it as critical to the primary goals to make them do so. Fundamentally, the way to make this system work faster is to use more robots,” said Cheung. “The overall strategy for scalability (of speed, size) is to be able to push the complexity of scale onto algorithms, for planning and scheduling as well as detecting faults and performing repairs.”
The robots developed by the lab took 256 voxels and assembled them into a passable shelter structure during a total of 4.2 days of work. Here’s what the start of that looked like (again, nowhere near real time):

Image Credits: NASA
If we’d sent them ahead to Mars or the moon a year ahead of a crew, they could build a dozen such structures twice the size with time to spare. Or perhaps they could affix the necessary plating to the outside afterwards and seal it up — that’s rather beyond the scope of the paper published today, but an obvious next step.
Though the robots have tethers running power to them in this lab environment, they’re being designed with battery operation or on-site power in mind. The fastener bot is already battery-powered, and the researchers are considering ways of keeping the walkers charged between or even during operations.
“We envision robots could be autonomously recharged at power stations or even perhaps beamed power wirelessly. As you mentioned, power could also be routed through the structure itself, which might be useful for outfitting the structure as well as powering the robots,” Gregg said.
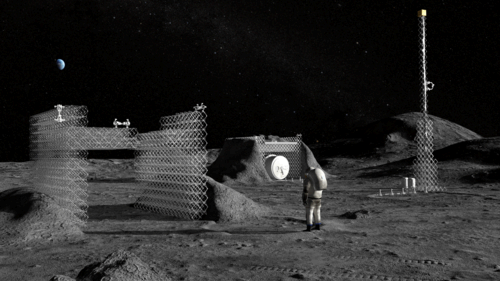
Concept illustration of ARMADAS building under astronaut supervision. Image Credits: NASA
Versions of the robot have already flown in space and done work in microgravity, so no worries on that score. And there’s nothing in principle preventing them from working in non-Earth gravities like the moon’s. That said, this is only the beginning — like revealing the existence of 2x4s and nails. There’s more on the potential, and concept illustrations of what they could build, at this NASA news post.
“The next versions of our robots for the laboratory environment will be faster and more reliable, based on our lessons learned with the first versions. We are very interested in understanding how different types of building blocks can be integrated into the structures to provide functional outfitting,” Gregg said.
Likewise research will continue on structures employing swarms of robots, not just a handful; a crude shelter might take two walkers four days, but something 10 times bigger might take 100 times longer. But many hands — especially robotic ones — make light work.